Abstract
When the friction stir welding (FSW) process is used in practice, defects appear under uncertain operating conditions. It is crucial to understand the basic mechanisms of defect generation so that it could be avoided. During the workshop, simplified models were developed for heat generation and plastic deformation, and attempts were made to find analytical and numerical solutions and continued until shortly after the workshop. We found that the unrealistic solution obtained during the workshop was due to the choice of a balance between inertial forces and plastic stress. In contrast, when inertia is negligible, physically reasonable solutions can be obtained for plastic deformation irrespective of the material compressibility. Investigating the dominant physical processes that drive this FSW process, the solutions from the simplified one-dimensional heat model and a two-dimensional non-Newtonian fluid model are also presented. The temperature distribution matches the results using direct numerical simulation and the experiment.
Content
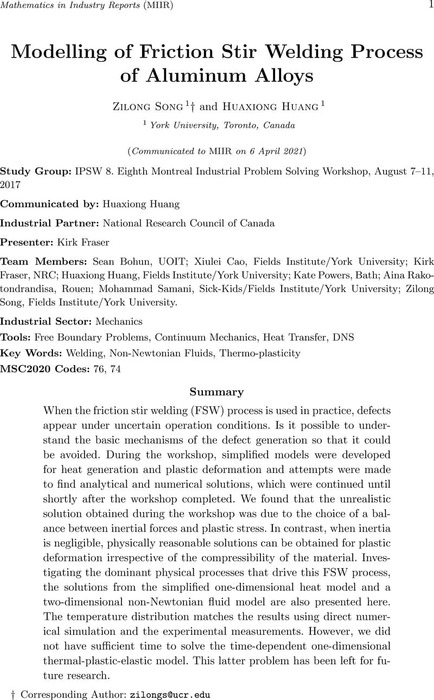